CADfix - CAD Translation, Repair, and Simplification Redefined
CADfix is an industry-leading software solution for CAD model translation, repair, healing, defeaturing, and simplification. CADfix is the go-to choice for professionals seeking to overcome challenges in 3D model data exchange and re-use between diverse engineering applications.
Key Features
Translate, Repair, and Simplify
CADfix empowers users to seamlessly translate, repair, and simplify CAD models for enhanced compatibility with CAD, CAM, and CAE applications. Break down barriers that hinder the re-use of solid models, ensuring a smooth transition across the product development lifecycle.
Geometry Processing for Advanced Simulation and Manufacturing
Unlock the potential of your CAD data with advanced geometry processing. CADfix facilitates the preparation of CAD models for advanced simulation and manufacturing, optimizing their performance in real-world applications.
Minimize Downstream CAD Model Rework
Say goodbye to extensive rework. CADfix minimizes downstream CAD model rework by addressing geometric and topological flaws within the CAD model. Enjoy improved efficiency and reduced project timelines.
Integrate and Automate CAD, CAM, and CAE Processes
Enhance your workflow with CADfix's ability to integrate seamlessly into PLM or workflow automation tools.
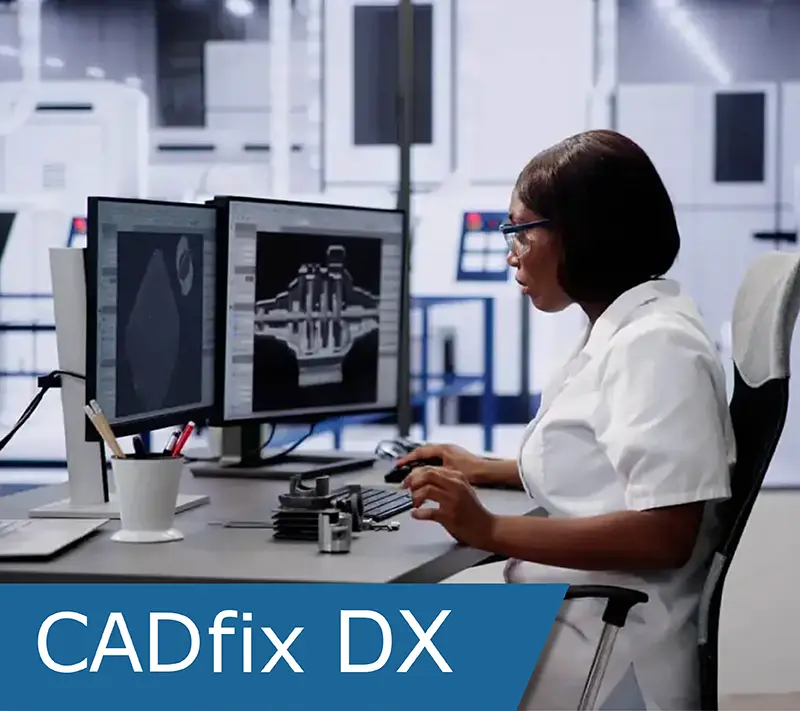
CADfix DX
Streamline Your CAD Data Exchange and Re-use
CADfix Data Exchange (DX) is an industry-leading software solution for CAD model translation, repair, healing, defeaturing, and simplification. CADfix is the go-to choice for professionals seeking to overcome challenges in 3D model data exchange and re-use between diverse engineering applications.
CADfix PPS
Equipment Model Simplification for Plant, Process, and Marine
CADfix PPS is the go-to solution for Plant and Process Simplification, offering a specialized set of tools to simplify overly complex and large mechanical CAD (MCAD) equipment models and reducing file size. CADfix PPS excels in reducing file size, streamlining equipment integration processes, and accelerating the journey to production.
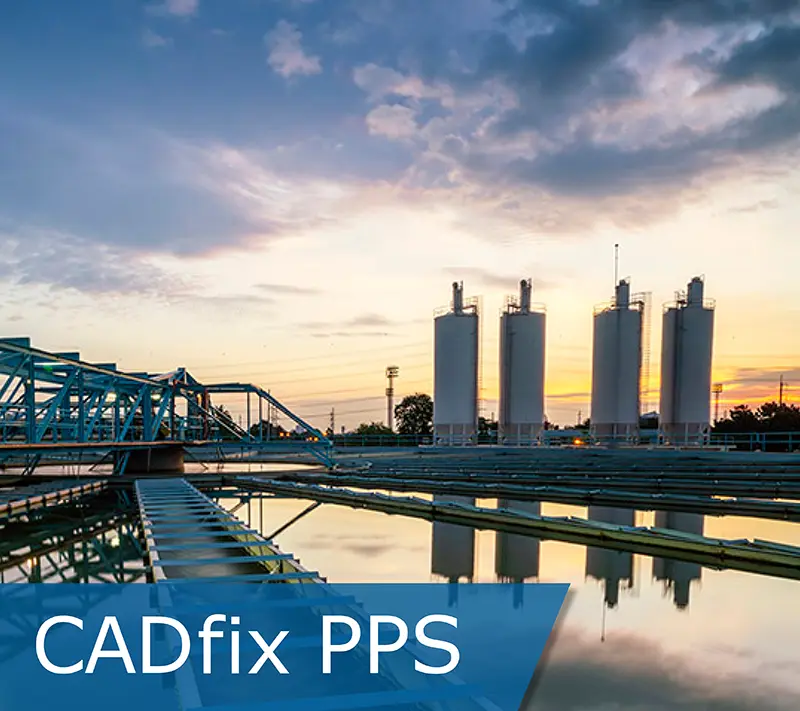
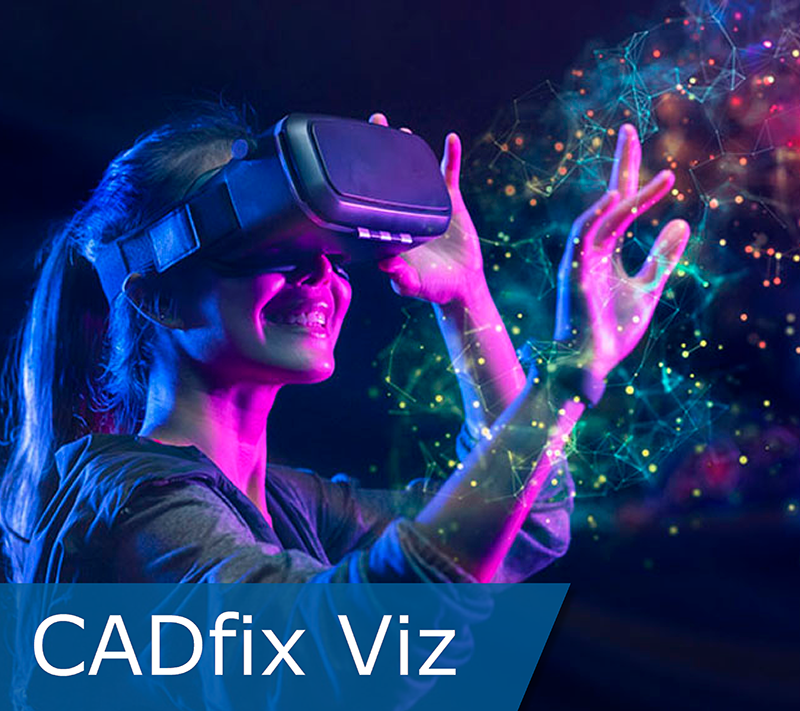
CADfix Viz
CAD Model Optimization for Visualization in VR/AR/MR
CADfix Viz takes the lead in optimizing 3D CAD model assets for use in virtual reality (VR), augmented reality (AR), and mixed reality (MR) applications. This powerful CAD to mesh conversion solution streamlines integration processes, maximizing the reuse of 3D digital assets and offering increased application interoperability. CADfix Viz is the key to saving valuable time while converting and repurposing complex CAD data for visualization applications.
CADfix STL
STL Generation
CADfix STL empowers users to generate high-quality, watertight, STL files with precise control over STL file creation, ensuring optimal triangle density and quality, and a mesh a suitable for their downstream needs.
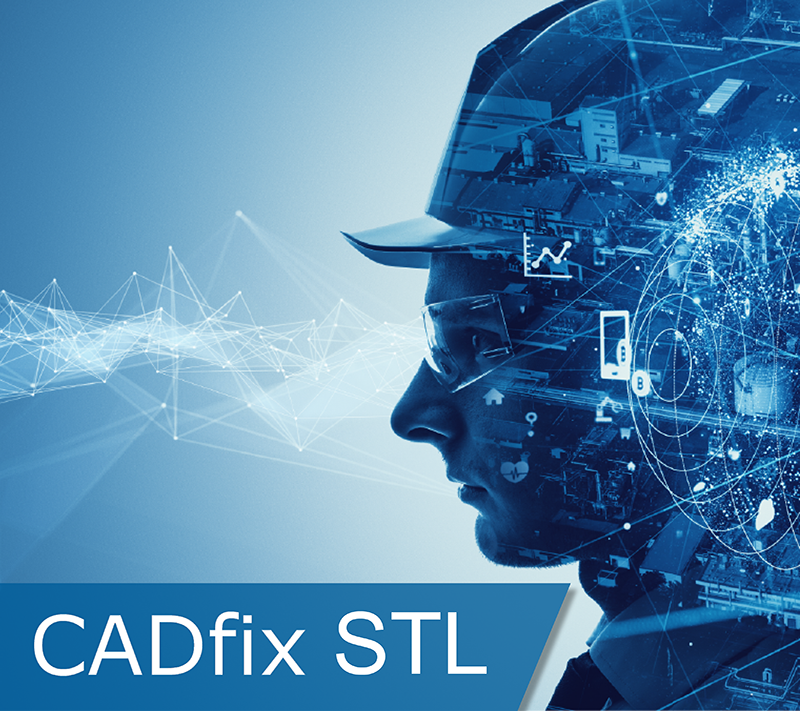
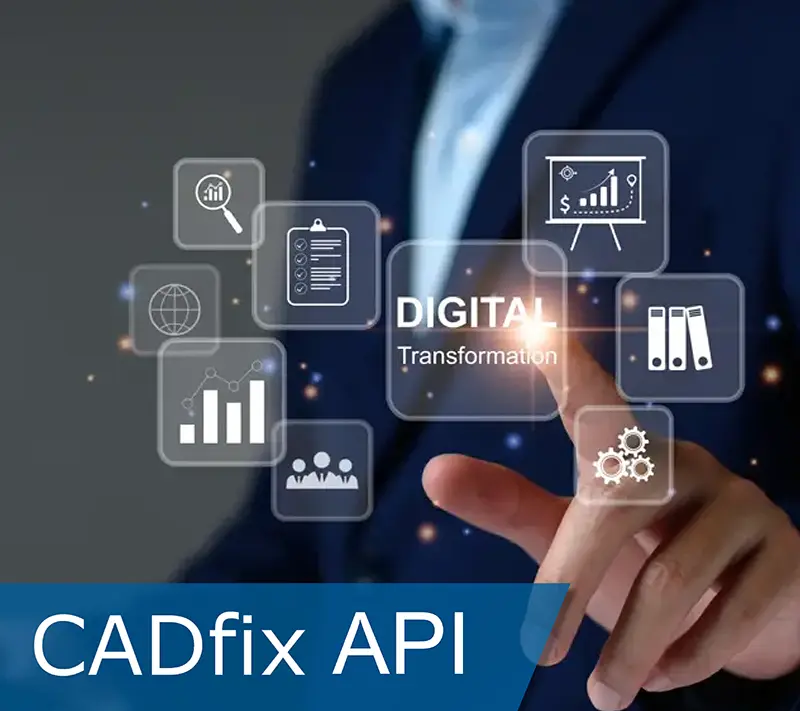
CADfix API
CADfix Modeling Engine & API
The CADfix geometry modelling engine, renowned for its robustness and versatility, is now available as an application development toolkit. This toolkit, accessible through the CADfix CFI (Custom Function Interface) application programming interface, provides a comprehensive library of geometry interrogation and processing functions, designed to empower developers and end users to create custom solutions.
CADfix Meshing
Optimize Your Engineering Workflow with CADfix Meshing
CADfix Meshing delivers powerful solutions for CAD repair, STL, and CAE meshing, streamlining the preparation of models for simulation and analysis. With advanced tools for automatic CAD repair, defeaturing, and high-quality mesh generation, CADfix ensures seamless integration into engineering workflows.

Contact Us Today
Explore how CADfix can revolutionize your CAD model translation, repair, healing, defeaturing, and simplification.